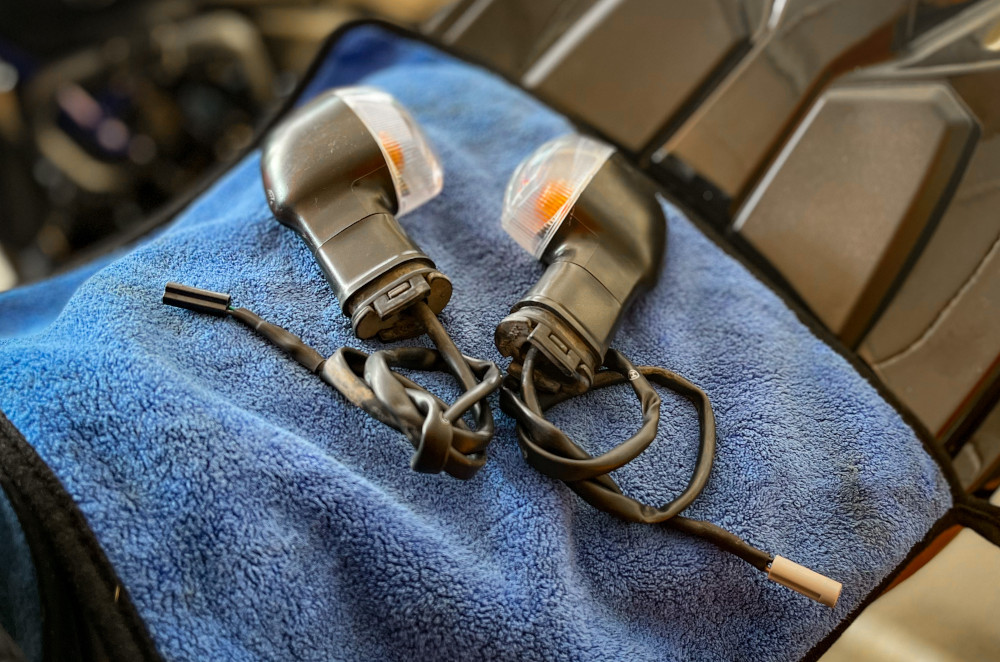
If you’re one who likes to customize or personalize your motorcycle with tasteful and functional upgrades like LED turn signals or mobile phone chargers, or you find yourself in need of replacing damaged electrical components with the need to transfer your stock connectors over, chances are you’ve had to deal with cutting and splicing wires. At first glance, it can seem rather daunting, however, in essence, it’s a rather straightforward job, especially if it’s a simple part like a turn signal.
Regardless of how easy the task may be, it’s always best to make sure to do it right the first time. It saves you the hassle of having to go back and do your work all over again. On top of that, if you’re like us, and want your bike’s wires looking clean and seamless all throughout, splicing your wires correctly keeps things neat and tidy. That said, simply follow the easy steps below to get it right the first time.
Have all the right tools
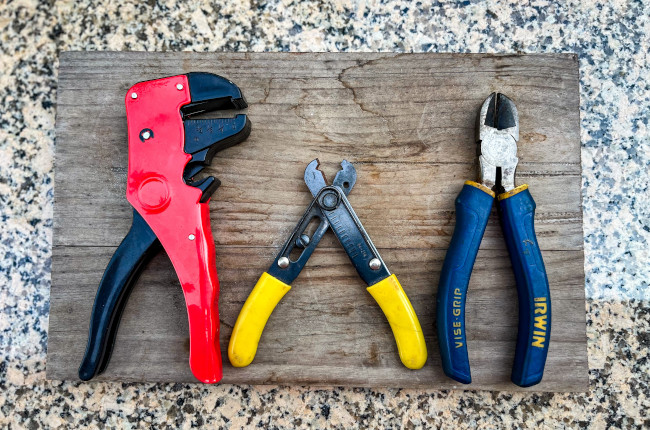
As is the case with all jobs, it’s absolutely essential to have the right set of tools to ensure you get the job done to a tee. Don’t expect to be able to cut and splice your wires with just a pair of scissors. To do it right, you’ll need a wire cutter, insulation stripper, some shrink tubing, a heat gun, and a lot of patience. Yes, you could get away with just a cutter and some electrical tape, but we want to make things look factory fresh now, don’t we?
Get the polarity right
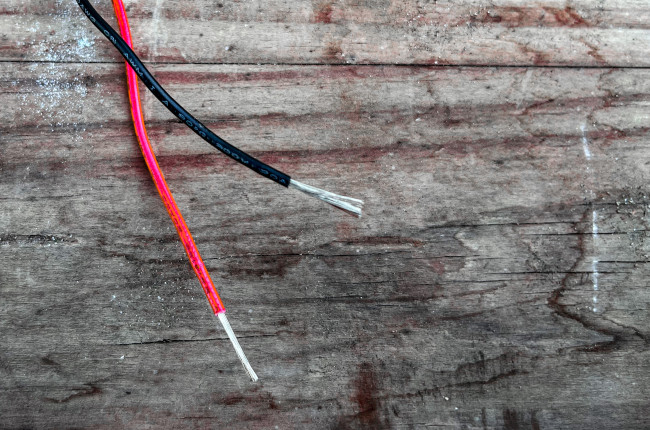
When installing turn signals or other electronic stuff, it’s always important to determine which side is positive, the part that gets power from the bike’s electrical system; and the negative side, or the ground. While most original, branded accessories usually have the positive side wrapped in a red or other brightly colored insulation, and the negative in either a black or dark brown insulation, this isn’t always the case on cheaper parts.
There are many ways to determine which side is positive and negative, the easiest of which would be to check for continuity with a multimeter. If you don’t have a multimeter, simply test it by putting the exposed wires on the terminals of your battery—it’s also best if you have a spare, used battery laying around. Usually, nothing bad happens if you mistakenly invert the polarity of turn signals; they just won’t work. Once you get the polarity squared away, it’s time to splice and dice.
Slice, splice, and test!
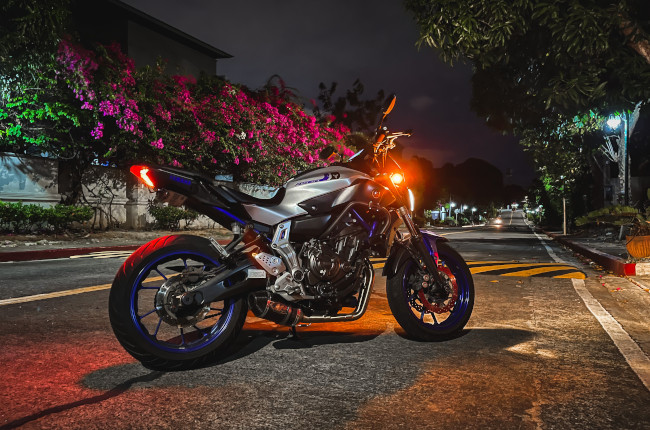
You’re going to want to start by cutting the wires to length, and exposing an adequate amount of copper. Do this with an insulation stripper. You can easily buy these tools online or in your nearest hardware store for a couple hundred pesos. It saves you a lot of time and makes sure you get the perfect length, the first time around. At this point, it’s also a good idea to cut the negative and positive wires to different lengths, to make sure that the two spliced areas don’t make unwanted contact in the event that the insulation around the spliced areas fails.
We recommend exposing around 5 to 7 mm of wire in order to get a strong and secure splice. Slide in some shrink tubing before you begin connecting the wires. Position the two wires at a 90-degree and begin twisting tightly and firmly. Once you’re done, slide the shrink tube over the spliced area and apply some heat with a heat gun. You should end up with a very clean and tidy connection. The last step would be to test your new connections and make sure everything’s working as it should.
Related Articles
-
Axial versus radial calipers - brake technology explained / Featured Article
Today, let’s talk about the differences between radially and axially mounted calipers, and determine the situations which are ideal for either.
-
Is your motorcycle out of warranty? Be sure to check these items ASAP / Featured Article
If your motorcycle is out of warranty, it’s now your duty to make sure you stay on top of its maintenance no matter what, or run the risk of facing a hefty repair bill.
-
Three reasons why you need a dual-sport motorcycle in your garage / Featured Article
Here are a few reasons why you need a dual-sport motorcycle in your garage, and a few reasons why they’re the most versatile machines on two wheels.
-
Think twice before installing these 3 motorcycle modifications / Featured Article
When it comes to upgrading your motorcycle, you may want to think twice before installing these 3 mods.
-
Have these documents ready when buying a used motorcycle / Featured Article
Here are some essential documents you need to ensure are complete before buying a used motorcycle.
Latest Features
-
Big bike versus small bike: which one is better for your lifestyle? / Featured Article
Here are a few tips to decide if you should get a big bike or small bike depending on your lifestyle.
-
Axial versus radial calipers - brake technology explained / Featured Article
Today, let’s talk about the differences between radially and axially mounted calipers, and determine the situations which are ideal for either.
-
3 things that make the Honda ADV 160 the perfect small-displacement all-rounder / Featured Article
Here are three reasons why the new Honda ADV 160 is one of the best small-displacement scooters in the market today.